Section 1: Introduction to Porous Sintered Materials
Section 2: Expanding Horizons – Applications and Design Advantages of Porous Sintered Materials
Section 3: Manufacturing Methods for Porous Sintered Materials
Section 4: Materials and Properties
Section 5: Designing and Specifying Porous Sintered Materials
Section 6: Secondary Operations for Porous Sintered Materials
Section 7: Testing of Porous Materials
Contact DALON for more details
Section 1: Introduction to Porous Sintered Materials
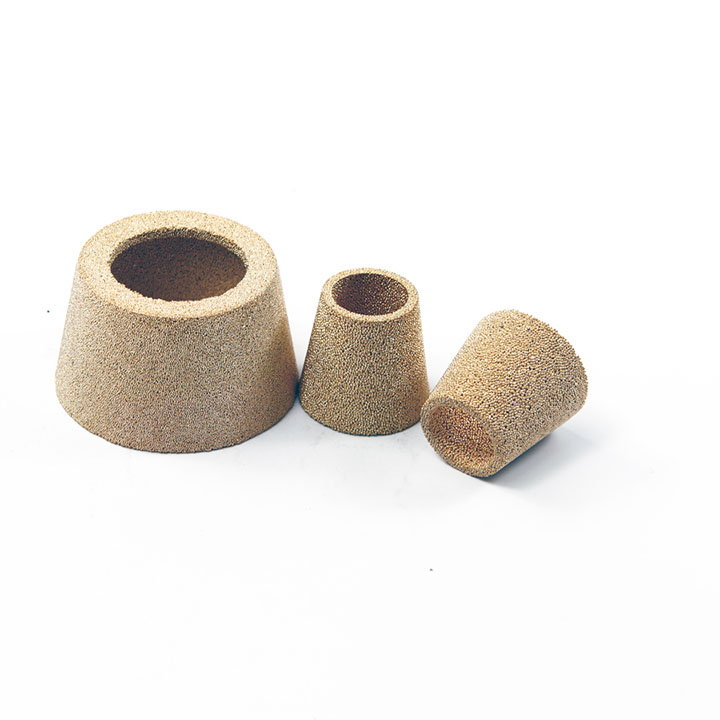
Welcome to the fascinating world of porous sintered materials! These engineered marvels, crafted from metal powders through the precision of powder metallurgy (P/M) techniques, offer unparalleled versatility and performance in a wide array of applications. From filtration to muffling, the unique properties of porous sintered metals can be tailored to meet the most demanding requirements.
In this section, we’ll demystify the key terms and concepts you need to understand the fundamentals of porous metal materials, their manufacture, and their applications. Let’s dive in:
- Pores: Imagine a sponge made of metal. The spaces within this metal sponge are called pores. These are the open volumes within the metal matrix, creating the porosity that gives these materials their unique characteristics.
- Interconnected Porosity: Unlike a random assortment of holes, the pores in sintered materials are skillfully engineered to connect, forming a network that allows fluid to flow seamlessly from one side to the other. This is in contrast to isolated pores, which are enclosed and don’t contribute to fluid flow.
- Percent Porosity: This is a measure of how much open volume exists within the material. It’s calculated as 100% minus the density of the part, including both interconnected and isolated porosity. This parameter is crucial for understanding the material’s capacity to filter or muffle.
- Particle Retention Rating: This rating tells you the size of particles that the material can filter out of a fluid. It’s a crucial factor in determining the suitability of a sintered material for specific filtration applications, and it’s defined by the efficiency of removing particles of a certain size.
- Micron Grade or Micron Rating: When we talk about the “Bubble Point,” we’re referring to this rating. It’s a measure derived from the size of the largest pore in the material, determined by the pressure needed to push air through that pore when submerged. This metric is vital for understanding the fineness of the filter.
- Permeability: Think of this as the breathability of the material. It’s the rate at which fluid flows through the porous material over a given area and pressure difference. High permeability means fluids can pass through more easily, a key consideration in designing filters or mufflers.
By grasping these fundamental concepts, you’re now better equipped to explore the vast potential of DALON porous sintered materials products. Whether you’re looking to achieve specific filtration efficiencies, tailor material properties for unique applications, or simply explore the cutting edge of material science, understanding these terms is your first step.
Section 2: Expanding Horizons – Applications and Design Advantages of Porous Sintered Materials
Porous sintered materials stand at the intersection of innovation and versatility, offering unique solutions across a myriad of applications. Engineered for excellence, these materials excel in separating, controlling, dampening, and distributing, among other functions. Here’s a deeper dive into the primary applications that showcase the breadth and depth of porous sintered materials’ capabilities.
1. Filters for Separating Solids from Liquids and Gases
From ensuring the purity of medical drugs to enhancing the performance of fuel oil burners, the filtration capabilities of porous sintered materials are unparalleled. Their precise pore size and strength make them ideal for applications including catalyst retention in chemical processes, polymer processing, and pressure regulation in sensitive instrumentation.
2. Fluid Flow Metering and Pressure Control
Accurate control over fluid flow and pressure is crucial in many industries. Porous sintered materials serve as the backbone for flow restrictors, calibrated leaks, and pneumatic delays, offering reliability in timing devices, gauge snubbers, and pressure equalization applications.
3. Storage Reservoirs for Liquids
Whether it’s for self-lubricating bearings or cooling devices, porous sintered materials provide innovative storage solutions. Their ability to act as reservoirs and wicks in heat exchange elements demonstrates their versatility in managing liquids efficiently.
4. Flame and Spark Arrestors
Safety in handling flammable gases is paramount. Porous sintered materials are trusted for their efficacy as flame and spark arrestors in welding torches and electrical enclosures, preventing accidents and ensuring safe operations.
5. Sound Dampening and Attenuation
In reducing noise pollution and enhancing acoustic quality, porous sintered materials offer effective solutions. Their application in pneumatic mufflers, silencers, and microphone attenuators showcases their capability to absorb and attenuate sound.
6. Gas Distribution and Sparging
The uniform distribution of gases is critical in processes like carbonation and oxygen stripping. Porous sintered materials facilitate this through applications in fluidized bed surfaces, air bearings, and spargers, ensuring efficient and even gas flow.
7. Media Retention
Serving as permeable barriers, these materials are essential in retaining media such as desiccants, getters, and purifiers. Their application in this area underlines their role in maintaining purity and effectiveness in various systems.
Design Advantages: Tailored to Perform
Beyond their diverse applications, porous sintered materials offer significant design advantages, including customizability, durability, cost-effectiveness, and environmental sustainability. These materials not only meet but exceed the demands of modern engineering challenges, offering solutions that are both innovative and practical.
By leveraging the unique properties of porous sintered materials, industries can unlock new levels of performance and efficiency. Whether it’s enhancing safety, improving process efficiency, or contributing to sustainability, the applications of these materials are as diverse as they are impactful.
Porous sintered materials are not just versatile in application but also unparalleled in the design advantages they offer. Whether in the realm of industrial filtration, sound dampening, or fluid flow control, the performance, availability, and cost benefits of these materials are instrumental in driving innovation and efficiency. Below, we delve into the primary applications and the pivotal design advantages that set porous sintered materials apart.
Unrivaled Performance
Porous P/M parts deliver exceptional performance, characterized by:
- Strength, Corrosion Resistance, and Durability: Each base metal powder brings its inherent high strength and durability to the final product, ensuring long-lasting performance in even the most demanding environments.
- Controlled Porosity and Permeability: Customization of porosity for specific filtration properties and permeability to meet precise flow specifications highlights the material’s adaptability to varied applications.
- Versatile Design Options: The ability to filter particles from 0.5 to 150 micrometers and manage flow rates from micro-leaks to high volumes opens up a wide range of application possibilities.
- Rigidity and Ease of Cleaning: Porous materials offer rigidity and shock resistance, essential for applications requiring robustness, along with ease of cleaning for maintenance.
Global Availability
- Broad Material Choices: From stainless steel and bronze to nickel alloys and precious metals, the use of commercially available powders ensures a wide variety of options for specific applications.
- Worldwide Manufacturing: Experienced P/M manufacturers around the globe can supply parts in various shapes and sizes, ensuring accessibility and timely delivery.
Cost-Effectiveness
- Efficient Production: Established volume production techniques and suitability for automatic assembly contribute to cost efficiency, making porous P/M parts economically viable.
- Precision and Minimal Waste: The net-shape design feature of P/M parts allows for close dimensional control with minimal machining required, reducing scrap loss and further optimizing costs.
Diverse Material Options
The portfolio of porous materials available recently by DALON includes:
- Stainless Steel (Type 316L SS), Bronze (Copper-10%Tin), PE, PP providing a rich selection for tailored applications.
Adherence to Industry Standards
Porous sintered materials comply with international standards for pore size, density, and permeability, such as:
- ISO 4003 for Mean and Maximum Pore Size
- ASTM E128-61 for Bubble Point Pore Size
- ISO 2738 for Density measurements
- ISO 4022 for Permeability
These standards ensure reliability and consistency across applications, reinforcing the material’s value proposition.
Section 3: Manufacturing Methods for Porous Sintered Materials
The production of porous sintered materials is a testament to the precision and adaptability of modern manufacturing techniques. Depending on the desired properties of the final product, such as part size, configuration, material, and degree of porosity, manufacturers may choose from several sophisticated processes. Here, we delve into two primary methods employed in the fabrication of these innovative materials.
1. Axial Compaction and Sintering
The Process: This method involves pressing metal powder into a die under high pressure, causing the particles to adhere at their contact points. This initial form, known as the “green” part, possesses enough strength to be handled post-ejection from the die. The green part’s strength before sintering hinges on various factors, including the metal powder’s characteristics and the forming pressure. Notably, porous metal parts are pressed at lower pressures compared to standard P/M structural parts to achieve the required porosity levels. Following compaction, the green parts are sintered under a controlled atmosphere, bonding the particles more firmly and significantly enhancing the part’s strength.
Materials and Advantages: Predominantly used for stainless steel and certain bronze parts, this method is favored for its high production rates, exceptional control over permeability, and excellent dimensional accuracy. The limitations in part size and shape align with those typical of the P/M manufacturing process.
2. Gravity Sintering
The Process: Employed primarily for materials that bond easily, such as certain types of bronze and plastics, this method does not apply external pressure to shape the part. Instead, powder graded for size is poured into a mold cavity shaped like the finished product. Upon heating to sintering temperature, metallurgical bonding occurs, forming solid connections at the particle contact points without melting the powder.
Design Considerations: Design engineers utilizing gravity sintering must envision the final part shape as enclosed by a mold, with an access hole for powder filling. The part must be designed for easy extraction post-sintering, typically requiring a draft of about 10 degrees. Given the variable nature of shrinkage and dimensional changes during sintering, part tolerances should be set liberally, with ± two percent as a general guideline for gravity sintered parts. To minimize the need for secondary processing, overall part lengths are recommended to be specified with generous dimensions.
Section 4: Materials and Properties
In the realm of porous sintered materials, the choice of material plays a pivotal role in determining the final product’s properties, applications, and performance. Our offerings include high-quality porous materials made from Stainless Steel Type 316L, Bronze (CuSn8/CuSn10), Polyethylene (PE), and Polypropylene (PP), each selected for its distinct advantages and suitability for various applications.
1. Stainless Steel Type 316L (UNS S31603)
Composition: 18% Chromium (Cr), 13% Nickel (Ni), 2% Molybdenum (Mo), 1% Silicon (Si), and a maximum of 0.03% Carbon (C).
Properties and Advantages: Chosen for its exceptional resistance to heat and corrosion, Type 316L stainless steel stands out among austenitic stainless steels. Its suitability for porous parts stems from the material’s wide availability in various particle sizes, catering to diverse specifications. With higher nickel and molybdenum content than standard stainless steel grades, Type 316L offers enhanced corrosion resistance, making it ideal for applications demanding durability and longevity. Porous parts made from Type 316L exhibit the same resistance to oxidation and strength at elevated temperatures as their fully annealed counterparts, albeit with slightly less corrosion resistance due to their porous nature.
2. Bronze (CuSn8 and CuSn10)
Composition: Predominantly Copper (Cu) with 8% or 10% Tin (Sn).
Properties and Advantages: Bronze, particularly in porous form, presents a cost-effective alternative to other sintered metals, attributed to the lower processing costs of gravity sintering spherical or cylindrical powders. While offering significant economic benefits, it’s important to note that the mechanical properties of porous bronze parts are generally lower than those of other materials requiring compaction before sintering. This material is frequently chosen for its balance between performance and cost, particularly in applications where superior mechanical strength is not the primary requirement.
3. Polyethylene (PE) and Polypropylene (PP)
PE & PP Properties: As thermoplastic polymers, both PE and PP offer unique advantages in the production of porous materials. Characterized by their lightweight, chemical resistance, and flexibility, these plastics can be engineered to achieve specific levels of porosity and permeability, making them suitable for a wide range of applications, from filtration to controlled release systems. Their inert nature and resistance to a broad spectrum of chemicals make them particularly appealing for medical and food-related applications.
Advantages: The key advantages of using PE and PP in porous applications include their versatility, cost-effectiveness, and suitability for applications requiring contact with sensitive substances. These materials are easily processed and can be tailored to meet specific design and performance criteria, offering a wide range of application possibilities.
Section 5: Designing and Specifying Porous Sintered Materials
Designing with porous sintered materials encompasses a spectrum of considerations aimed at harnessing their unique performance characteristics for specific applications, primarily in fluid control. Understanding these materials’ capabilities allows for the creation of components that excel in filtration, flow control, distribution, and leveraging porosity to meet exacting requirements.
Performance Characteristics
The design process starts with a clear grasp of the desired function, typically related to fluid control, categorized into:
- Filtration: Achieving separation with minimal pressure drop. Porous sintered products excel in depth-filtration, offering superior dirt-holding capacity and fine degrees of filtration by optimizing pore size distribution and part dimensions.
- Flow Control: Porous sintered parts can precisely regulate fluid flow, varying porosity to adjust pressure drop with high accuracy, ideal for creating precision leaks and control elements.
- Distribution: Ensuring uniform fluid flow across a broad area, critical for applications such as spargers and air bearings. Design specifications focus on volume, gas pressure, and desired bubble size or flow rate.
- Porosity: The interconnected open area within the material, crucial for defining filtration efficiency and flow control. Specifications often involve a “bubble point” test to measure the pore size distribution, guiding the design for optimal performance.
Mechanical Properties
- Strength and Shape: The density and annealed base metal properties dictate the strength of a porous P/M part. The manufacturing method influences the optimal part shape, balancing design flexibility with manufacturability constraints.
Design and Specifying Guidelines
To effectively specify porous sintered materials, designers should provide comprehensive details, including:
- Application Purpose: Clearly define the function of the porous part (filtration, fluidization, etc.).
- Materials to be Processed: Identify what will pass through the part, considering the size and nature of particles or fluids.
- Operating Conditions: Outline corrosion challenges, temperature ranges, pressure conditions, and potential contaminants.
- Physical Specifications: Detail dimensions, shape, tolerances, and mounting or support requirements.
- Performance Requirements: Specify desired flow rates, allowable pressure drop, and system pressure, emphasizing functional needs over non-critical specifications.
Engaging closely with the manufacturer is crucial, leveraging their expertise to refine specifications and achieve optimal design outcomes. This collaboration ensures that the final product meets performance expectations while navigating manufacturing capabilities and constraints effectively.
Section 6: Secondary Operations for Porous Sintered Materials
Secondary operations play a crucial role in the final performance and application-specific customization of porous sintered materials. DALON have rich experiences and established procedures ensure that every component not only meets design specifications but also surpasses application expectations. Here’s an overview of the essential secondary operations we employ:
1. Press Fitting and Sinter Bonding
- Integration Technique: We efficiently combine machined parts with porous materials through sinter bonding and press fitting, leveraging the deformability of porous materials for a secure fit. This process involves either integrating a machined part into the sintering mold or press fitting a sintered porous part into a hardware component, followed by a secondary sintering cycle to form a strong metallurgical bond.
2. Machining
- Precision and Porosity Maintenance: While porous parts achieve high uniformity post-sintering, certain applications require machining for dimensional accuracy or specific geometries. To retain porosity, we use sharp tools and specific techniques, including a careful post-machining treatment to reopen any smeared pores and meticulous cleaning to ensure the integrity of the porous structure.
3. Welding
- Durable Assemblies: Our porous stainless steel structures can be assembled with precision through welding, suitable for joining porous to porous or porous to machined parts. Utilizing inert arc welding and consulting with experienced professionals ensures high-quality joins, crucial for the functionality and longevity of the final product. Porous plastic elements are also effectively joined using ultrasonic welding or adhesive bonding, tailored to enhance joint strength without compromising the part’s functional area.
4. Cleaning
- Maintenance and Reusability: Depending on their application and material composition, our porous parts can be either disposable or designed for reuse through appropriate cleaning methods. Techniques include solvent cleaning, backflushing, or thermal methods to remove contaminants, ensuring the parts’ continued performance and safety in their respective applications.
5. Storage and Handling
- Preserving Integrity: To maintain the highest quality and performance readiness, porous parts are stored in optimal conditions and handled with the utmost care, especially for critical applications in medical, semiconductor, and other sensitive industries. Our handling processes, including organic-free and cleanroom-type procedures, ensure the parts remain contaminant-free and ready for use in even the most demanding environments.
Section 7: Testing of Porous Materials
Testing porous sintered materials is critical to ensuring their performance meets the specific requirements of their intended applications. Unlike standard tests that focus on physical dimensions, the qualification tests for controlled porosity powder metallurgy (P/M) parts are primarily application-oriented, highlighting the necessity of performance-based evaluations.
Performance Testing: The Key to Qualification
- Application-Specific Tests: The effectiveness of porous P/M parts is best determined through performance tests under conditions that mimic actual use. This approach is particularly vital for flow control elements, where functionality is influenced by both the P/M part and its assembly within the device.
- Joint Test Procedures: Establishing test protocols requires collaboration between the customer and the P/M parts maker. Typically, both parties set up identical test stands calibrated with standard parts to measure critical performance metrics like flow rate and pressure drop. These tests ensure that every component functions as expected within its operational environment.
Typical Test Setups
- Standard Testing Configuration: A common setup involves passing fluid through the porous part to a flow meter, then to the atmosphere, measuring controlled fluid input pressure, flow rate, and pressure drop.
- Alternative Arrangements: In scenarios where collecting gas from parts like long tubes is challenging, flow meters may be positioned before the porous part, with readings adjusted for pressure changes.
- Time Delay Applications: Parts designed for time-delay functions are tested for the specific time required for pressure to change under simulated conditions, rather than steady-state flow, ensuring accuracy in timing applications.
International Standards and Mechanical Property Testing
Several international standards guide the testing of permeable sintered metal materials, ensuring consistency and reliability across the industry:
- ISO 2738: Determines density, oil content, and open porosity.
- ISO 4022: Measures fluid permeability.
- ISO 4003: Establishes bubble test pore size for identifying maximum pore size.
- ASTM E128: Provides a standard test method for maximum pore diameter and permeability of rigid porous filters for laboratory use.
Mechanical properties such as tensile, burst, collapse, shear strengths, and ductility are also critical metrics, indicating whether appropriate sintering conditions were applied during processing. These tests verify the material’s structural integrity and suitability for specific applications.