Sintered parts with steam treatment
Steam treatment can effectively improved the mechanical and corrosion resistance of sintered parts.
For steam-treated parts, the density of the parts and the steam treatment process have a great impact on the treatment effect.
At the same time, some post-sintering processes such as shaping, vibration deburring, grinding, etc. will refine or even partially refine the pores of the sintered pores.
Therefore, it is necessary to conduct some consideration on the effects of these aspects, so as to select and formulate appropriate steam treatment processes according to different preliminary production procedures.
Introduction
For iron-based powder metallurgy materials, which due to their structures contain certain pores, compared with dense materials with the same composition, they have the characteristics of lower hardness, poor corrosion resistance and air tightness.
After steam treatment, they will A hard and dense oxide layer composed mainly of Fe3O4 on its surface, which can greatly improve the hardness, compressive strength, rust resistance, wear resistance and gas resistance of the sintered iron-based material.
For powder metallurgy parts with a density higher than 7.0g/cm3, it can only improve the corrosion resistance of the parts and has little impact on the mechanical properties.
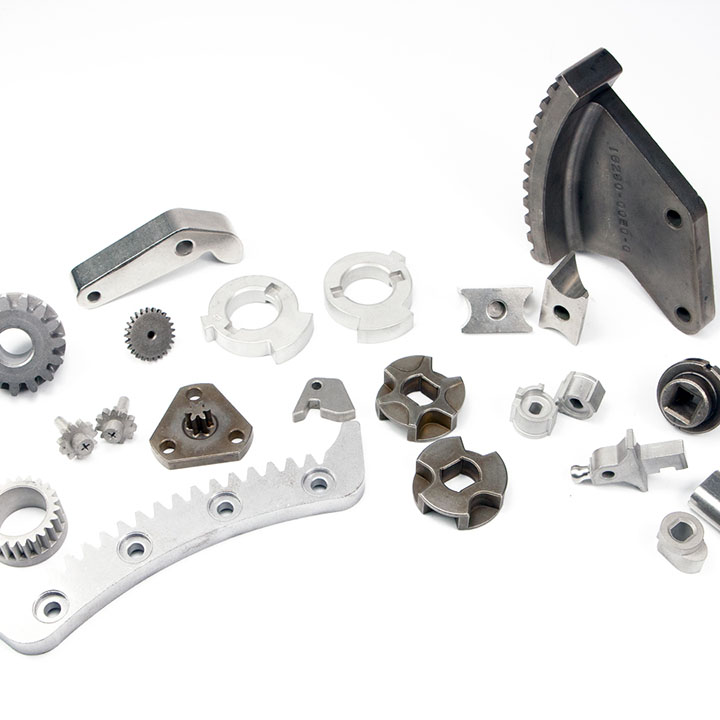
Experimental methods
The specific method is: continuously extract 16 samples (numbered 1 to 16 respectively) in batch production, and sinter them in the same furnace at the same time (sintering temperature 1120°C, time 30 minutes, density after sintering 6.9±0.03g/cm3).
Test group as Table 1. Treatment process as Figure 1.
The steam pressure during the treatment process between 30±4KPa.
Table 1. Testing Groups
Test Group | Sample Batch | Sample Type | Steam Treatment |
---|---|---|---|
A | #1,#2,#3,#4 | Sintered parts | Two-stage |
B | #9,#10,#11,#12 | Shaping, vibration deburring parts | Two-stage |
C | #5,#6,#7,#8 | Sintered parts | One-stage |
D | #13,#14,#15,#16 | Shaping, vibration deburring parts | One-stage |
Steam Treatment Process Curve
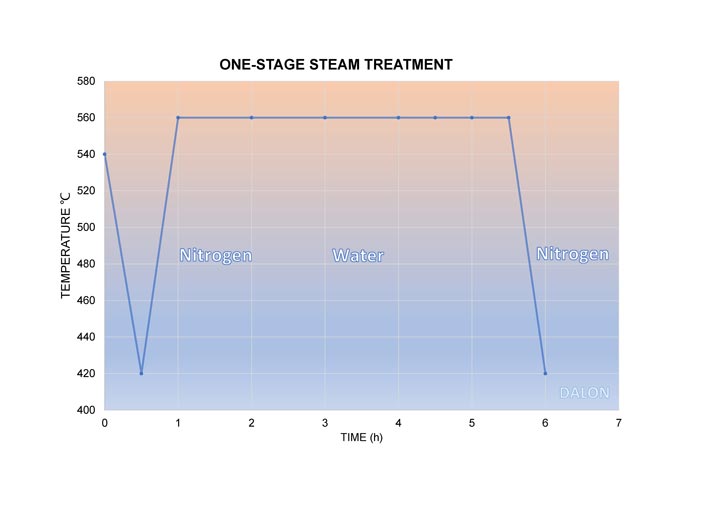
Figure 1.
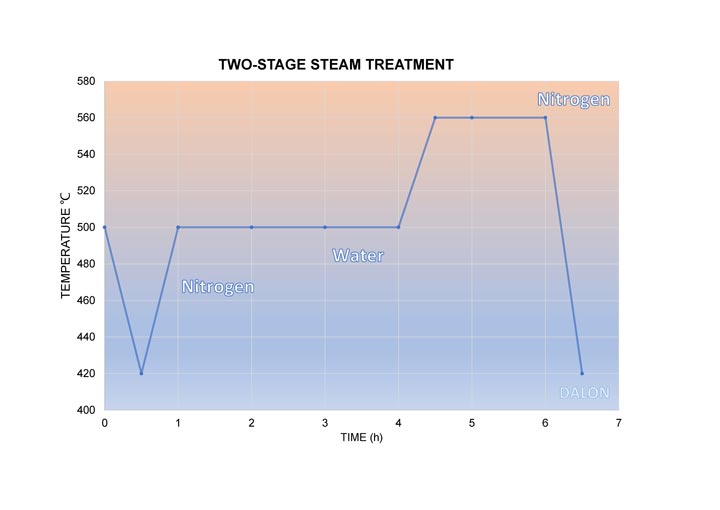
Table 2. Testing Groups
Test Group | Sample Type | Steam Treatment | Average Weight Grain | Average Hardness |
---|---|---|---|---|
A | Sintered parts | Two-stage | 2.7% | 87.6HRB |
B | Shaping, vibration deburring parts | Two-stage | 2.37% | 88.6HRB |
C | Sintered parts | One-stage | 2.41% | 86.6HRB |
D | Shaping, vibration deburring parts | One-stage | 1.52% | 80.6HRB |
Testing Analysis & Result
Table 2 shows the relevant data after steam treatment in four groups of experiments A, B, C, and D.
It can be seen from it that whether the one-stage or two-stage steam treatment process is used, the weight gain rate of the sintered parts after steam treatment is higher than that of the Shaping, vibration deburring parts.
The main reason for the large size of vibration deburring parts is that some of the open pores will be closed or refined after shaping and vibration deburring.
In this way, in addition to the closed pores during steam treatment, those that have been refined the pores will also be closed relatively quickly, thus hindering the reaction from proceeding to deeper parts, and ultimately the weight gain rate will be smaller than that of sintered parts.
Two-stage steam treatment process
For samples that use a two-stage steam treatment process, since they are first steam treated at 500°C for 1.5 hours and then raised to 560°C for treatment, the reaction speed at 500°C is much gentler than that at 560°C, even for samples with sealing effect such as shaping and vibrating parts, the steam can have sufficient time to react with it at this temperature without clogging the pores, so that the sintered parts and the shaping and vibrating parts have a large weight gain rate and the difference is not big.
One Stage steam treatment process
For samples treated with one stage of steam, since the steam treatment is carried out at 560°C, the reaction speed is faster, so that the refined pores in the shaping and vibrating parts are quickly closed, so that the reaction only occurs when the samples is relatively small. It is carried out in shallow parts, and the generated oxide film is very thin. Compared with sintered parts, because the pores of sintered parts are larger, even if the reaction is faster, the pores will not be closed in a short time, and the reaction can still proceed in deeper parts. In this way, after a period of steam treatment, the weight gain rate and hardness of the sintered parts are obviously much greater than those of the shaping and vibrating parts.
Conclusion of Treatment
For the same kind of samples, the weight gain rate of two-stage heating steam treatment is greater than that of one-stage heating treatment, and the corresponding hardness is also higher.
For sintered parts, the weight gain rate and hardness are not much different when using one-stage heating and two-stage heating for steam treatment. However, for samples that have sealing effects such as shaping, vibration deburring, and grinding after sintering, Generally speaking, the weight gain rate and hardness of the two-stage heating treatment are significantly greater than that of the one-stage heating treatment. Therefore, for those samples that have hole sealing treatment after sintering when the requirements for hardness, air tightness, etc. are high, it is better to adopt a two-stage heating treatment method.
Enquiry to DALON today!
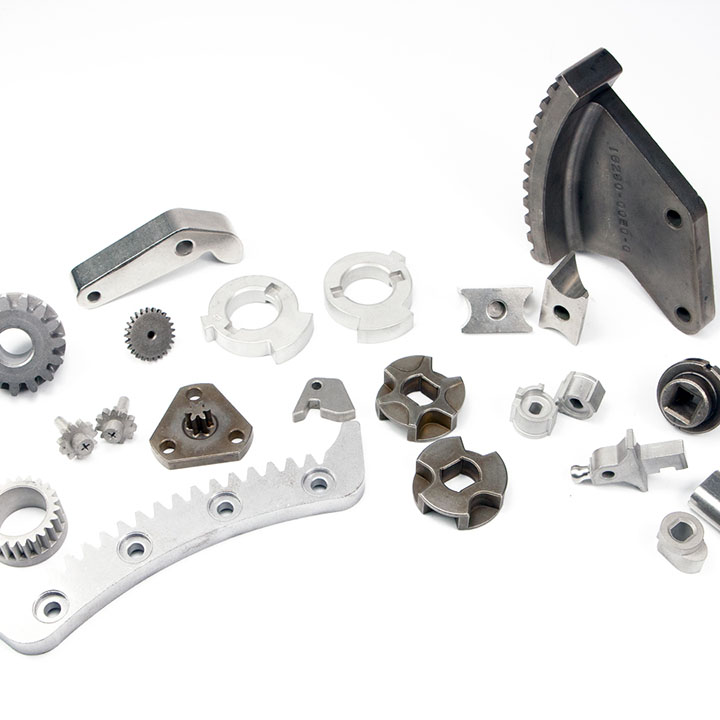