Example Requirement:
- Life expected: 5000h
- Self-lubricated plain bearings (No need add lubrication of the plain bearings in the assembly process)
- Maximum temperature operation (cyclical peaks): 150°C
- Shaft diameter: Ø12mm – Steel SAE 1045
- Maximum external diameter of the bearing: Ø32mm
For the specific requirements above listed, selecting the appropriate self-lubricated plain bearing involves considering materials that can withstand the operational conditions, especially the high temperatures and the expected lifespan without additional lubrication. Here’s a recommendation based on the criteria:
- Life Expectancy: Self-lubricated composite bearings are designed to last the required 5000 hours of operation without the need for maintenance or additional lubrication, meeting your life expectancy requirement.
- Self-Lubrication: These plain bearings incorporate materials such as PTFE (polytetrafluoroethylene), graphite in their matrix, which provides inherent lubrication throughout their service life.
- Temperature Resistance: Composite materials are chosen to withstand high temperatures, with some variants capable of handling up to 250°C, well above the 150°C cyclical peak temperature specified. This makes them suitable for high-temperature applications.
- Dimensional Requirements:
- Shaft Diameter: For a Ø12mm steel SAE 1045 shaft, the bearing’s internal diameter would be designed to closely match or slightly exceed 12mm to ensure a proper fit without excessive friction.
- Maximum External Diameter: With a maximum external diameter limit of Ø32mm for the bearing, a composite bearing can be selected or custom-designed to fit within these spatial constraints while providing the necessary load support and alignment.
- Material Compatibility: Ensure the composite material is compatible with a steel SAE 1045 shaft, particularly in terms of wear resistance and potential for galvanic corrosion, if applicable.
- Load and Speed: The bearing selection should also consider the operational load and speed. Composite bearings are generally suitable for a wide range of loads and speeds but confirming compatibility with specific application’s requirements is crucial.
More Questions:
For the specified applications requiring self-lubricated plain bearings capable of operating at high temperatures (up to 150°C) with a specific life expectancy and dimensional constraints, let’s address each of the additional questions based on the initial recommendation of self-lubricated composite plain bearings:
• Which plain bearing are recommended for these applications?
DALON Self-lubricated Composite Plain Bearings are recommended, as previously detailed. These bearings are suitable for applications with high-temperature requirements, limited space, and a need for self-lubrication to avoid maintenance.
• What are the requirements of shaft (surface finish and shaft tolerances)?
- Surface Finish: The surface finish of the shaft is crucial for optimizing the bearing life and performance. For self-lubricated composite bearings, a shaft surface finish of Ra 0.2 to Ra 0.8 micrometers (µm) is typically recommended. A smoother finish helps in reducing wear and extending the bearing life.
- Shaft Tolerances: The shaft tolerance for composite plain bearings generally falls within the h6 to h9 range, according to ISO tolerance classes. This range provides an optimal balance between tight fit and allowance for thermal expansion or material compression.
• What is the thickness of the end shield indicated to lock the bearing?
The thickness of the end shield (or retaining structure) that locks the bearing in place depends on several factors, including the axial loads, the method of fixation, and the design of the assembly. A general guideline is to design the end shield thickness to be robust enough to support the axial loads without deformation. This might range from 1.5mm to 3mm, but the exact thickness should be calculated based on the specific application loads and conditions.
• What is the solution to lock the bearing in the end shield?
To lock the bearing in the end shield effectively, consider the following methods:
- Press Fit or Interference Fit: This method involves designing the housing bore with a slightly smaller diameter than the outer diameter of the bearing, creating an interference fit when the bearing is pressed into the housing. This is a common method for securing bearings and can be very effective for applications with moderate loads and speeds.
- Retaining Rings or Snap Rings: These can be used in a groove at the end of the housing to mechanically retain the bearing. This method allows for easier replacement of the bearing but requires careful design to ensure the groove and ring do not compromise the integrity of the housing or the bearing fit.
- Adhesive or Locking Compounds: For additional security or in applications where mechanical retention methods may not be suitable, specific high-temperature adhesives or locking compounds can be used to secure the bearing within the housing. These materials should be selected based on compatibility with the operating temperatures and materials.
- Set Screws or Clamping Rings: For some designs, set screws or clamping rings that tighten around the outside of the housing can provide an effective means of securing the bearing, especially when axial loads are significant.
Please refer to DALON tools for more information about Mechanical Design.
Each locking solution has its advantages and considerations, such as ease of assembly, load support, and maintenance requirements. The choice of method should be based on the specific demands of the application, including load characteristics, assembly and maintenance practices, and environmental conditions.
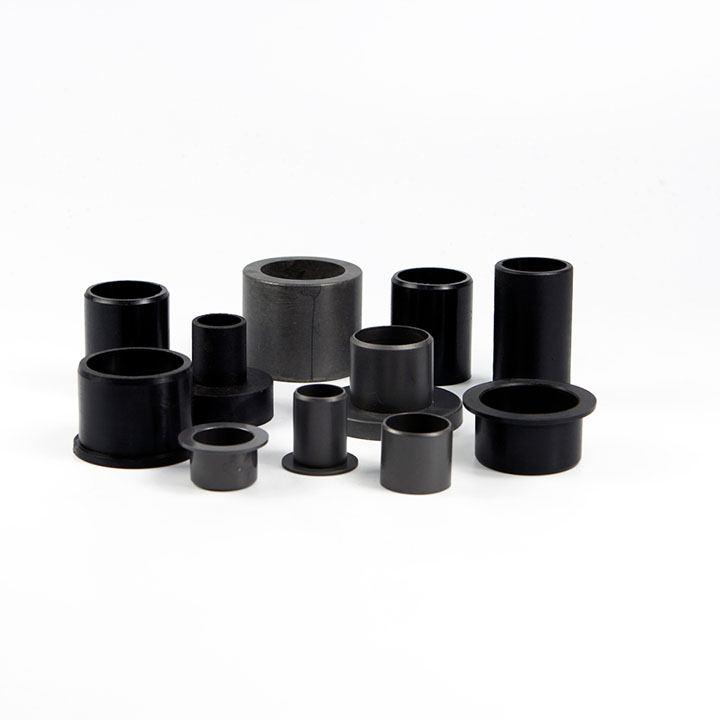
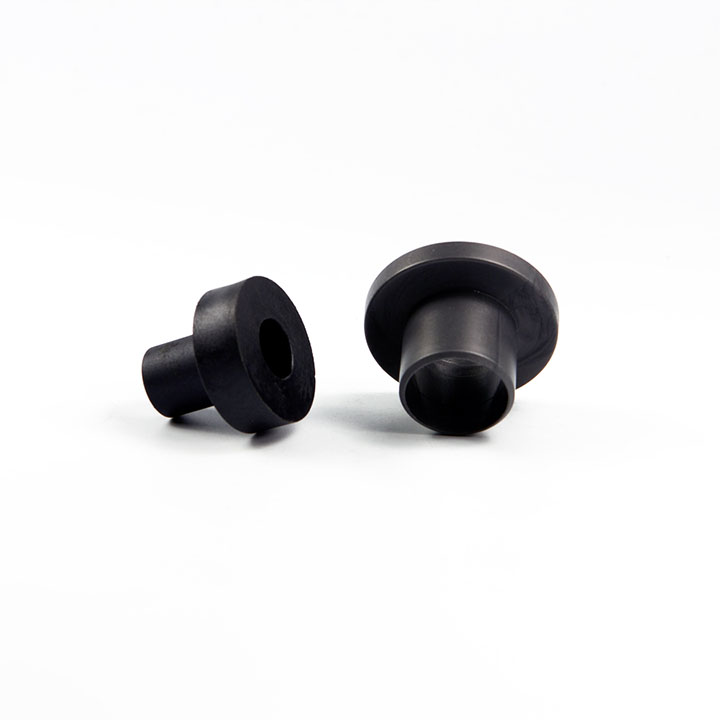
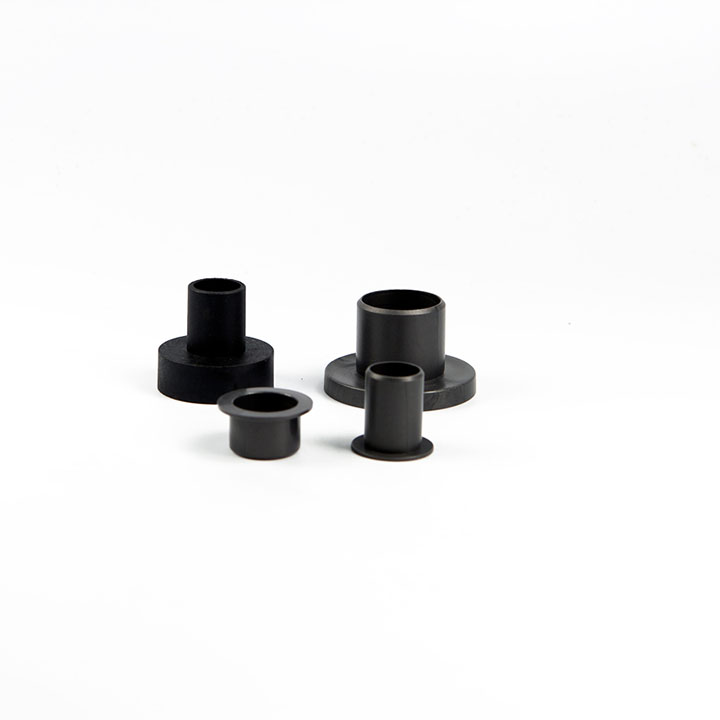